Rebar For Garage Slab: A Comprehensive Guide
As an Amazon Associate, I earn from qualifying purchases.
Is Rebar for Garage Slab Required?
Rebar reinforcement of concrete slabs is required in most applications. While concrete has high compressive strength, it lacks tensile strength. You can enhance the overall tensile strength of concrete by incorporating rebars in it. As such, rebars reinforce the slab and ensure the structural integrity of the concrete floor.
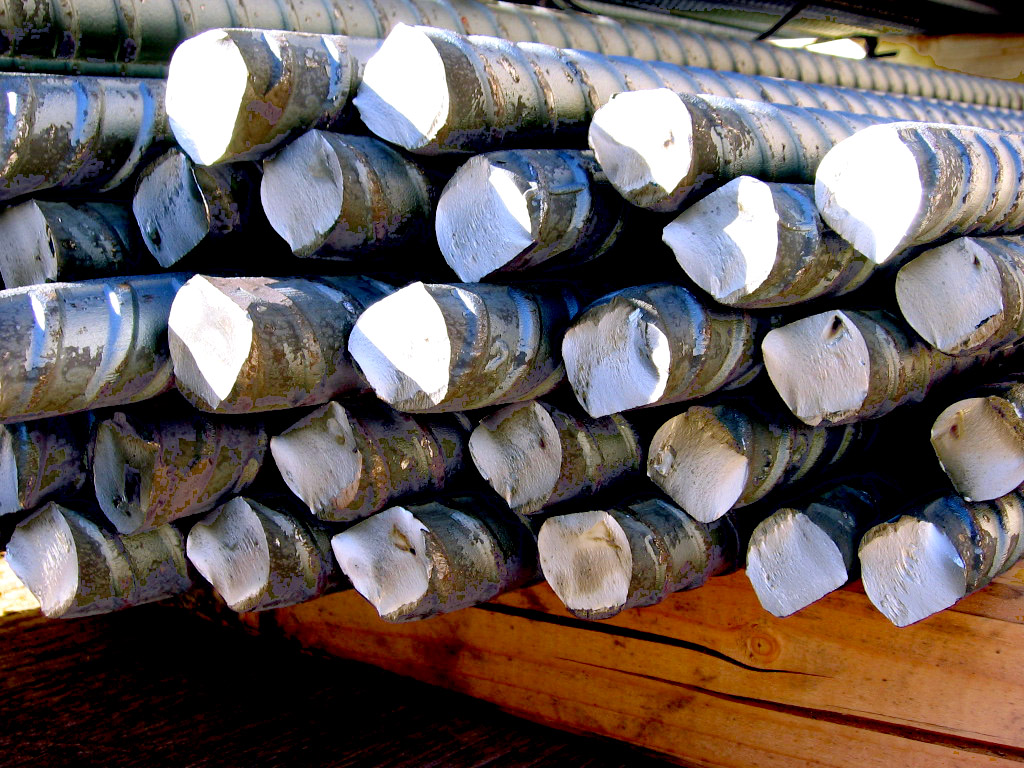
However, rebar for garage slab, 4 inches or less in thickness is not recommended. Instead, wire or fiber mesh should be used to strengthen the concrete and minimize cracking.
On the other hand, rebar for garage slab, 5 inches or thicker, is highly recommended to provide adequate load-bearing capacity and prevent structural failure.
This is the short & sweet answer. Read on to learn more about the role of rebar in garage slabs and how it can impact your construction project.
What is Concrete & What is Reinforced Concrete?
Cement is a key ingredient of Concrete but cement by itself is not concrete.
“Concrete is a composite material composed of fine and coarse aggregate bonded together with a fluid cement (cement paste) that hardens (cures) over time.”
Source: Wikipedia
The concrete mix
“.. is about 10 to 15 percent cement, 60 to 75 percent aggregate and 15 to 20 percent water. Entrained air in many concrete mixes may also take up another 5 to 8 percent.”
Source: The Portland Cement Association
The concrete mix is a slurry and can be poured into almost any structural element such as slabs, beams, columns, etc. Over 4 weeks this pliable slurry cures into a rock solid mass with great strength…compressive strength to be precise.
Concrete Slab Strength
The strength of a building material is measured in PSI (pounds per square inch). This is the load the material, in this case concrete, can withstand before breaking or crumbling.
Compressive Strength is the ability of concrete to withstand a load that is pressing into the concrete. Concrete slabs, such as in garage floors have pretty high compressive strength.
The compressive strength of concrete depends on a host of factors. Water to water-to-cement ratio in the concrete mix is possibly the most important factor. As a thumb rule, the compressive strength of concrete goes up as the water-to-cement ratio goes down.
Section R402.2 of the 2021 International Residential Code (IRC) specifies “Minimum Specified Compressive Strength” for garage floor slabs. It also recommends that the water-to-cement ratio be kept at 0.5 or lower. At this compressive strength level the garage slab can take all the load of your cars, furniture, what have you.
Tensile strength, on the other hand, is the ability of concrete to resist breaking or cracking under tension. In simpler words, high tensile strength is flexibility and low tensile strength is brittleness.
Concrete with a compressive strength of 4000 psi may have a tensile strength of just 400 psi.
Reinforced Concrete Slab
A concrete slab on grade such as a garage floor or a driveway is subjected to a compressive load whenever a vehicle is parked on it. At the same time, it is also subjected to bending stress as the edges are fixed to the grade but the center is being pushed down by the weight of the vehicle.
Bending stress results in compressive stress in the upper section of the slab and tensile stress in the lower section of the slab. Since the tensile stress of normal concrete is low the slab on grade will fail by cracking.
To prevent this it becomes necessary to reinforce the concrete with a material that has high tensile strength. The embedding of the reinforcing material results in a reinforced concrete slab.
Rebar or any other type of reinforcement in garage concrete slabs is required mainly to handle flexural or tensile stresses. Such stresses may also be caused by uneven shifting of the grade below or large temperature fluctuations.
To learn more about concrete garage floors check out my earlier blog post 7 Important Things To Know About A Concrete Garage Floor.
What Happens if You Do Not Use Rebar in Concrete Slabs?
Rebars in concrete slabs serve one of the following two functions:
Rebars Provide Structural Tensile Strength
As mentioned earlier, concrete has great compressive strength but poor tensile strength. Concrete reinforced with rebar is necessary to increase the ability of the slab to withstand flexural or tensile stresses.
In the case of a garage slab on grade, tensile stresses are created in the slab if the subbase is poorly prepared. The grade itself may become unstable due to soil erosion or seismic activity.
For example, in case of heavy rains or even mild earthquake tremors, the grade below the subbase and the garage slab may sink unevenly. If the slab has not been reinforced using rebars or other reinforcing elements, the concrete slab may suffer structural damage and cracking.
Rebars for providing structural tensile strength are most effective when they are placed in the middle of the lower half of the concrete slab. However, they serve no purpose if they are right at the bottom of the concrete slab.
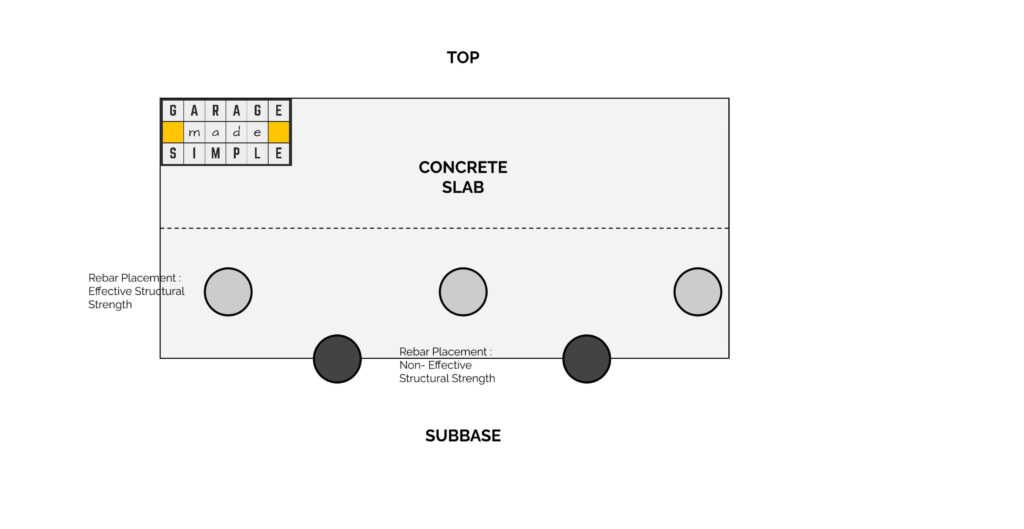
Rebars Limit the Crack Width in Concrete
Concrete, almost always, cracks. The cracks are the result of stresses caused by concrete shrinkage during curing, expansion & contraction during temperature fluctuations, uneven sinking of subbase and grade, etc.
Rebars or any form of reinforcement can not stop the occurrence of cracks. They have no role in the crack development process. However, rebars, along with contraction & expansion joints, can and will limit the expansion and growth of the cracks in the garage concrete floor.
In general, there are two options for controlling cracks in slabs-on-ground: 1) control the location of cracking by installing contraction joints (does not control crack widths) or 2) control crack widths by installing reinforcement (does not control crack location).
Source: FOR CONSTRUCTION PROS
Why Rebar for Garage Slabs (4″ or thinner) are Not Required?
When the concrete contractors (or you) say that they (or you) are pouring a 4″ thick garage slab, what they (or you) mean is that 4″ is the “nominal” size. In other words, the height of the slab form is 4″.
Real Garage Slab Thickness
So the number quoted for a garage concrete slab thickness is the “nominal” thickness. This is not the “real” thickness.
“Concrete floors and slabs on grade are called out by their “nominal” thickness. Just like a 2×4, a four inch thick slab is only 3-1/2” thick. This is so the edges can be formed by using a 2×4 and the area to be prepared can be graded off the same way, by using a 2×4.”
Source: Hansen Pole Buildings
Slabs generally cure to a thickness less than poured and often in a non-uniform manner across the area of the slab.
Rebar Diameter
Standard Rebar size starts at #3 (3/8″) diameter. In most residential projects #4 (1/2″) diameter and #5 (5/8″) diameter are used. In commercial and large-scale projects much higher # rebars will be used based on the engineering specifications.
Embedding of Rebar in Concrete Slab
If a Rebar is not properly embedded in the concrete then its effectiveness in enhancing the tensile strength of the concrete slab is severely diminished.
Concrete Gripping the Rebar
The Rebar is not smooth. Instead, it has ridges. The role of the ridges is to let the concrete “grip” the rebar. This gripping is what allows the transfer of tensile stress from the concrete to the rebar.
If the rebar is not embedded properly in the concrete then there will be no “gripping” and no transfer of tensile stress from concrete to rebar.
Rebar Exposed to the Elements
Moreover, if the rebar is not embedded deep enough in the concrete, it may get exposed to the elements, especially moisture, salt, air, and chemicals in the atmosphere.
A rebar that gets exposed to the elements may rust and weaken. Adequate coverage of the rebar with concrete is essential. Else the rebar may do more damage than good to the garage slab on grade.
The rule of thumb in structural engineering regarding rebar reinforcement is that the rebar should be embedded at least 2″ on all sides.
Quite obviously a 4″ thick garage slab (real thickness 3 1/2″) is just not thick enough to embed a #4 (1/2″) diameter rebar by 2″ on all sides. A rebar in a 4″ (nominal thickness) garage slab would be an absolute waste of money.
How do you Strengthen a 4″ Thick Garage Slab Without Rebar?
The best ways to provide the required structural strength (both compressive and tensile) in a standard concrete garage slab on grade is:
- Ensure the concrete meets the “minimum specified compressive strength” by ICC. A compressive strength of 3,000 to 3,500 psi is adequate for a garage slab.
- To achieve the minimum compressive strength above ICC recommendations the water-to-cement ratio should be 0.5 or less.
- Ensure that the sub-base uses the right grade of gravel and is compacted well. A stable strong sub-base will significantly minimize the flexural load on the garage slab on grade
- Use a thin welded wire mesh as reinforcement to limit the expansion and growth of cracks in the garage slab. Wire Mesh is made from thin stainless steel wires formed into a grid pattern.
Wire Mesh
A Wire Mesh for Concrete Slab does the same job as Rebar, except that it is much thinner and therefore can add less strength than rebar. However, they are ideal for a 4″ thick garage slab.
Fiber Mesh
Fiber Mesh, a recent development, is an alternative to Wire Mesh. Different types of fibers such as glass, steel, and synthetic or natural fibers are distributed evenly in the wet concrete. It saves time and money. However, many contractors believe that Fiber Mesh is not as effective as Wire Mesh.
Is Rebar for a 6″ Thick Concrete Slab Required?
Concrete slabs for garage floors are typically 4″ thick. This thickness is adequate for bearing the load of cars, trucks and SUV’s. Moreover, a garage is an enclosed space and is protected from extreme climatic conditions.
On the other hand, a concrete driveway is completely exposed to the elements. Moreover, there is a good chance that it will have heavy vehicles such as garbage trucks, dump trucks, etc. driving and parking on it. It is best to go for a 6″ thick slab in this scenario.
Keeping in view the load carrying capacity requirement a 5″ – 6″ thick concrete slab must use rebars. Rebars help the concrete to deal with tension stress and provide greater tensile strength to minimize cracking.
A wire mesh will not provide the required strength and the slab is very likely to crack and fail.
The most commonly used rebar sizes for slabs up to six inches thick are #5 and #4. In inches the diameter of a #5 rebar is 5/8″ and that of a #4 rebar is 1/2″.
Rebar Spacing for Concrete Slab
The spacing of the rebar should increase to between 18 and 24 inches apart for slabs between four and six inches thick. However, many engineers and contractors use a rule of thumb of keeping the rebar spacing to 2 – 3 times the slab thickness.
A tighter spacing will naturally increase the strength of the slab. At the same time it will increase the cost as well!
Types of Rebars
Rebars come in a variety of profiles and materials. Some of the common types include:
- Plain Round Rebars: Plain round bars are the basic and most widely used type of rebar. They provide general reinforcement for concrete structures, including driveways.
- Deformed Rebars: Deformed rebar, also known as ribbed rebar, has ridges or deformations on its surface. These deformations enhance the bond between the rebar and the concrete, providing better load transfer and increasing the strength of the reinforced concrete.
- Epoxy-Coated Rebars: Epoxy-coated rebar is protected by a layer of epoxy coating. This coating helps prevent corrosion, making it particularly suitable for concrete slabs exposed to moisture or salt, such as those in coastal areas.
While mild steel and carbon steel rebars are commonly used, other options such as galvanized rebars, epoxy-coated rebars, glass-fiber-reinforced-polymer (GFRP) rebars, and stainless steel rebars are used in projects where corrosion may be a critical issue.
The choice of rebar type depends on the specific requirements of your driveway project. For example, stainless steel rebars are the most resistant to corrosion but are also the most expensive. It is best to listen to the advice of your driveway contractor or consultant.
It is important to follow code requirements when using rebars in concrete slabs. For example, in some areas, bonding the steel reinforcement in an exterior concrete pad is required.
Rebars can be pre-cut and shaped to the desired size and shape. They must be placed on chairs and held together using wire mesh or zip ties, before the concrete pour.
This will ensure that the rebars do not end up being at the bottom of the slab (where they are not effective) and the uniform spacing is maintained.
Comparing Rebar with Other Reinforcement Methods
Rebar vs. Wire Mesh
Rebar and wire mesh are both used to reinforce concrete, but they serve different purposes.
Rebar provides superior tensile strength and is ideal for areas subjected to heavy loads and stresses. It is typically used in thicker slabs and structural elements.
Wire mesh, on the other hand, is easier to install and is often used in thinner slabs to control cracking and improve the overall integrity of the concrete. While wire mesh is less expensive and quicker to install, it does not offer the same level of strength as rebar.
Rebar vs. Fiber Mesh
Fiber mesh consists of synthetic fibers mixed into the concrete, providing uniform reinforcement throughout the slab. It helps reduce shrinkage cracks and improves the durability of the concrete.
However, rebar offers greater structural support and is essential for load-bearing applications. Fiber mesh is often used in conjunction with rebar to enhance the performance of the concrete, but it cannot replace rebar in high-stress scenarios.
Rebar vs. Post-Tensioning
Post-tensioning involves the use of high-strength steel tendons that are tensioned after the concrete has cured. This method allows for thinner slabs and greater spans without the need for additional support.
Rebar, while effective in providing tensile strength, does not offer the same level of flexibility and efficiency as post-tensioning.
Post-tensioning is often used in commercial and industrial applications where large, open spaces are required. However, it is more complex and expensive to implement compared to traditional rebar reinforcement.
Thank you very much for reading the post. I do hope you found it informative and useful.