Garage Slab Foundation: Best Option in Most Cases!
As an Amazon Associate, I earn from qualifying purchases.
The garage slab foundation is a commonly used essential component of garage construction. It is possible to construct a garage without a foundation or use other types of garage foundations, but the garage slab foundation is, without doubt the most popular choice, especially for a detached garage.
The garage slab foundation is not only easy to install but is also the most affordable choice. To be fair, the garage slab foundation is not the best option for a large garage intended for heavy loads. However, it will work just fine for most 2 car garages.
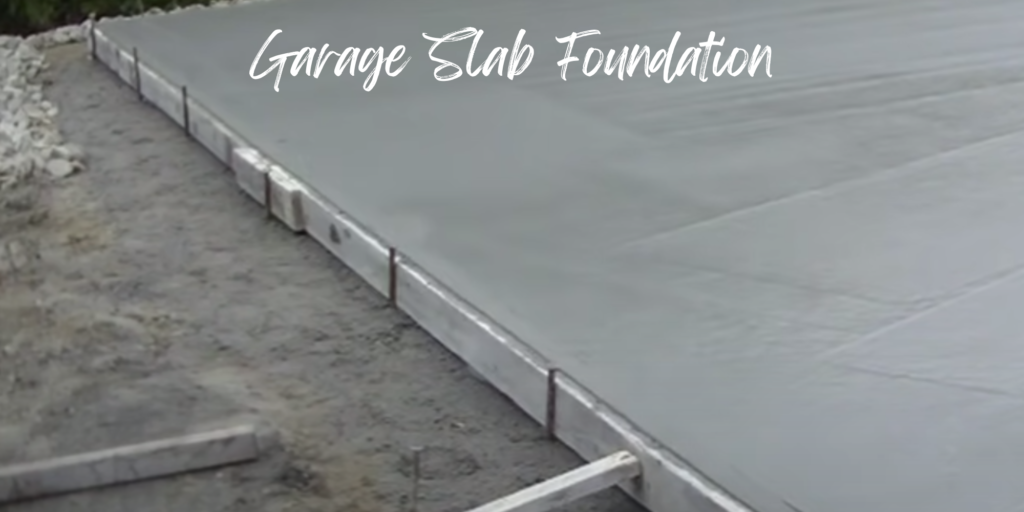
What is a Garage Slab Foundation?
A garage slab foundation is a continuous, monolithic concrete slab that supports the garage structure. The garage slab foundation is a popular choice for residential projects.
It is poured on top of a prepared subgrade, which consists of compacted soil and gravel. The slab is typically 4-6 inches thick and is reinforced with steel rebar to provide additional strength and rigidity.
The primary purpose of a garage slab foundation is to evenly distribute the weight of the garage and its contents, including vehicles and storage items.
This prevents the garage from settling or shifting, which could lead to structural damage.
Key Components of a Garage Slab Foundation
- Subgrade: The subgrade is the prepared earth on which the sub-base and base are placed. It must be level and compacted so that it does not shift or crumble.
- Sub-base & Base: A gravel layer is placed over the subgrade. Not only does it give strength to the soil support system but it also provides much-needed drainage.
- Vapor Barrier: A vapor barrier is placed over the gravel layer to prevent moisture from rising from the ground and into the concrete.
- Concrete Slab: The concrete slab is the main component of the foundation. It is poured over the vapor barrier and reinforced with rebar to increase its strength and durability.
Benefits of a Garage Slab Foundation
There are several benefits of a garage slab foundation. Some of the important ones are:
- Stability: A slab foundation provides a solid and stable base for the garage structure, preventing shifting and settling. This is especially important in areas with expansive soils or high water tables.
- Durability: A garage slab foundation is highly durable and can withstand heavy loads. It is ideal for parking cars and storing stuff that you can never find space for.
- Moisture Resistance: A well-constructed garage slab foundation can help to prevent ground moisture from infiltrating the garage, protecting belongings from damage.
- Cost-effectiveness: Garage slab foundations are typically more cost-effective than other types of foundations, such as T-shaped or pier and beam foundations.
Different Types of Garage Slab Foundations
There are a few different types of garage slab foundations. Some of the more popular ones are:
Traditional Poured Concrete Slabs
Traditional poured concrete slabs are the most common type of garage slab foundation. This method involves pouring a concrete mixture directly onto a prepared surface, creating a solid, level foundation.
A slab-on-grade foundation can be a floating garage slab that is suitable for small garages with very light loads. For medium size garages with moderate loads it is better to go for a monolithic garage slab.
Poured concrete slabs are cost-effective, reliable, and widely used for residential garages due to their durability and straightforward installation process.
Reinforced Garage Slab Foundations
Reinforced garage slab foundations offer enhanced strength and resilience, making them ideal for regions prone to soil movement, seismic activity, or heavy loads.
These foundations incorporate reinforcement materials like rebar (steel bars) or fibers within the concrete mix, providing added protection against cracks and structural stress.
Precast Garage Slab Foundations
Precast garage slab foundations are pre-manufactured in controlled environments and then transported to the construction site.
This process results in consistent quality, faster installation, and minimal disruption to the surrounding area.
Precast slabs are also ideal for challenging or complex projects, such as those with uneven terrain or limited access.
Post-Tensioned Garage Slab Foundations
Post-tensioned garage slab foundations utilize high-strength steel tendons within the concrete, allowing for greater spans and reduced thickness.
As a result they are the best option for specific architectural and engineering requirements, such as garages with large open spaces or garages that need to be built over existing structures.
How Thick Should a Concrete Garage Slab Foundation Be?
The thickness of the concrete slab is crucial as the thickness directly affects the strength and functionality of the garage slab foundation.
When it comes to taking a decision on the slab thickness there are several factors to consider as under:
Soil Type
Expansive or clay soils can cause cracking in a slab foundation due to their tendency to move and shrink. To prevent this, a thicker slab is required. Stable, well-compacted soils, on the other hand, may allow for a slightly thinner slab foundation.
Garage Size
A larger garage will require a thicker slab to support its weight. This is because the weight of the garage is distributed over a larger surface area, resulting in less pressure per square inch on the slab.
Intended Use
If you plan to use your garage for heavy-duty purposes, such as storing heavy equipment or vehicles, you will need a thicker slab to support the additional weight.
Industry Standards
Engineering organizations have established guidelines and standards for the appropriate thickness of a concrete garage slab foundation. These standards consider factors such as soil bearing capacity and the weight the foundation needs to support.
It is important to adhere to these guidelines to ensure that the foundation can withstand the loads imposed by the garage structure and its contents over time.
How to Determine the Right Thickness
The IRC code requires the minimum slab thickness to be at least 3 1/2″.
NOTE: Section 1907.1 of the 2021 International Building Code (IBC) specifies that the thickness of concrete floor slabs supported directly on the ground shall not be less than 3 1/2″.
However, in practice most garage concrete slabs are at least 4″ thick. In fact, it is best to have the garage slab foundation 6″ thick so that you can reinforce it with rebars.
Does a Garage Slab Foundation Need Rebar?
Rebar, or reinforcement bars, are essential for strengthening concrete slabs, including a garage slab foundation. Concrete has great compressive strength but lacks tensile strength. This is where rebars come in. Steel has very high tensile strength.
The combination of concrete and steel rebars creates a formidable reinforced concrete slab.
Rebar is indispensable in garage slab foundations under specific circumstances, such as:
- Areas with unstable soil
- Regions prone to seismic activity
- Garages supporting heavy loads, such as multiple vehicles or heavy equipment
Benefits of Rebar in a Garage Slab Foundation
- Enhances tensile strength, reducing the risk of cracks and ensuring long-term stability
- Reinforces concrete, helping to distribute the load uniformly and preventing localized stress points
- Increases the foundation’s ability to withstand loads and environmental stressors
Is the Garage Floor the Same as the Garage Slab Foundation?
No, your garage floor is not the same as your garage slab foundation. The garage floor is the topmost layer of the garage, the surface you drive on and walk on. The garage slab foundation is the concrete slab underneath the garage floor that provides support and stability.
It’s important to understand the difference between these two terms because a stable foundation is essential for a level and durable garage floor. If the foundation is uneven or weak, the garage floor can crack, sag, and develop other structural problems over time.
Here is a simple analogy: Think of your garage floor as the icing on a cake and the garage slab foundation as the cake itself. The icing is the visible part of the cake, but the cake itself is what gives the icing its structure and support.
Similarly, the garage floor is the visible part of the garage, but the garage slab foundation is what gives the garage floor its strength and stability.
Is Gravel Under Concrete Garage Slab Foundation Required?
Yes, gravel under concrete garage slab foundation is required. Gravel is required for
- Providing a Stable Base: Gravel distributes the weight of the concrete evenly, preventing it from settling or cracking.
- Improving Drainage: Gravel allows water to drain away from the foundation, preventing it from pooling and causing damage.
- Reducing the Risk of Soil Shifting: Gravel helps to prevent soil erosion, which can cause the foundation to shift and settle.
Pouring a Concrete Garage Slab Foundation
Step 1: Excavation
Excavate the area where your garage will stand to the depth specified in your foundation plans (typically 12″). Remove any debris and create a level surface.
Step 2: Compaction of Subgrade
Use heavy machinery to compact the soil thoroughly. This will prevent settling and ensure a stable base for the foundation.
Step 3: Geotextile Fabric (Optional)
While not always necessary, laying a geotextile fabric on the compacted subgrade can further enhance stability and drainage.
Step 4: Gravel Placement
Spread a layer of gravel, typically 4 to 6 inches thick, evenly over the subgrade. Use a well-graded, compactable type of gravel, such as crushed stone.
Step 5: Gravel Compaction
Use a mechanical compactor to compact the gravel layer thoroughly. This will eliminate air gaps and create a solid sub-base for the concrete slab.
Step 6: Leveling
Use a straight board or screed to level the gravel layer and ensure that it is even throughout. Maintain the specified thickness throughout. Top us with a couple of inches of sand, which should also be compacted.
Step 7: Moisture Control
In areas with high groundwater levels, place a vapor barrier over the compacted base to prevent moisture from seeping up into the concrete.
Step 8: Placing Rebars
The rebars should be placed on “chairs” to ensure that they are at the right height within the slab. Further make sure that the longitudinal and lateral rebars are tied together at the cross points to prevent movement during the pour.
Step 9: Concrete Pouring
Once the gravel base is properly prepared and inspected, you can proceed with pouring the concrete for your garage slab foundation. Make sure to order the best concrete mix for your garage slab foundation.
Expert Tips
- When excavating the area for your garage slab foundation, be sure to remove any soft or unstable soil. If you encounter any problems, such as bedrock or underground water, consult with a qualified professional.
- When compacting the soil and gravel, it is important to use a heavy-duty compactor that is appropriate for the size and type of material being compacted.
- If you are using geotextile fabric, be sure to overlap the fabric at the seams and extend it at least 6 inches beyond the perimeter of the garage slab foundation.
- After pouring the concrete, it is important to cure it properly. This involves protecting the concrete from moisture and heat for several days. The curing time is typically 28 days.
By following these steps, you can prepare a solid, durable concrete garage slab foundation that will support your garage.
Thank you very much for reading the post. I do hope you found it informative and useful.